CIP - Performance and Sustainability
Most businesses in the food and beverage industry have some sort of clean in place (CIP) system.
CIP is a critical part of a hygienic process. The CIP Kitchen ensures the process equipment remains clean, and ensures there’s no carryover or cross-contamination from product to product (or batch to batch).
Traditionally, the standard CIP kitchen was single-use. Water and cleaning chemicals (caustic and acid) are used once and then sent to drain after completing each stage of the CIP cycle.
A more modern approach is a re-use CIP system where water and chemicals are recycled across multiple uses. For example, the final water rinse of a CIP cycle is recycled back to a rinse water tank, where it is reused as the first flush in the next CIP cycle.
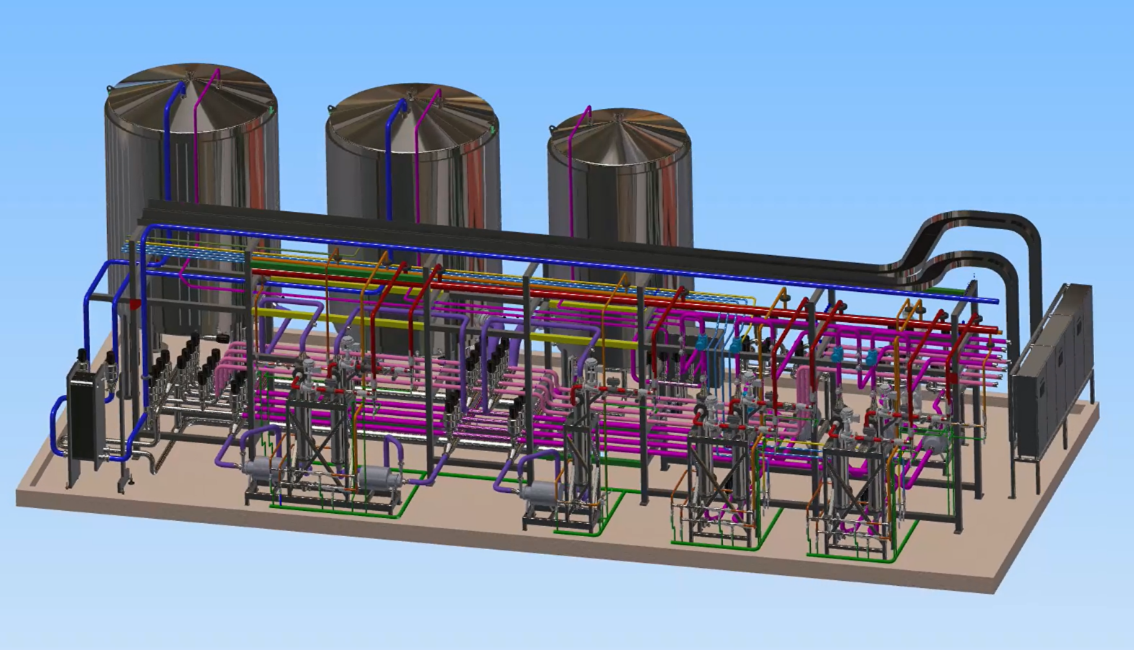
3D model of reuse CIP kitchen with water, acid and caustic recovery
Many plants still use single-use systems, and even the companies with re-use systems are unsure how their CIP system is performing.
It has been estimated that on average, a food and beverage plant will spend 20% of each day on cleaning equipment.
These plants also use a considerable amount of energy, water, and chemicals. In the dairy sector, CIP can account for 9 to 26% of the energy consumption on a site.
On average, a food/beverage plant will spend
%
of each day cleaning equipment
In the dairy sector, CIP accounts for up to
%
of the sites ENERGY consumption
Why look at CIP Performance?
CIP can be a source of hidden inefficiencies and waste within a process. CIP cycles are run longer than necessary, hot water is unnecessarily used, or chemicals are overdosed, ‘just in case’ or ‘because that’s how we’ve always done it’ – which is effectively time and money, going literally down the drain.
Improving the performance of our CIP systems is perhaps not the first thing that comes to mind when it comes to process improvements, but there are tremendous opportunities for manufacturers.
The impact on the bottom line, with savings to; water, waste, chemicals and energy is an obvious one, but there is also sustainability performance.
In today’s world, being sustainable is not just a nice to have for marketing, it is a business development strategy and competitive advantage.
If we look at some of the key areas of sustainability and ownership cost an improvement to the CIP will potentially impact four of these elements.
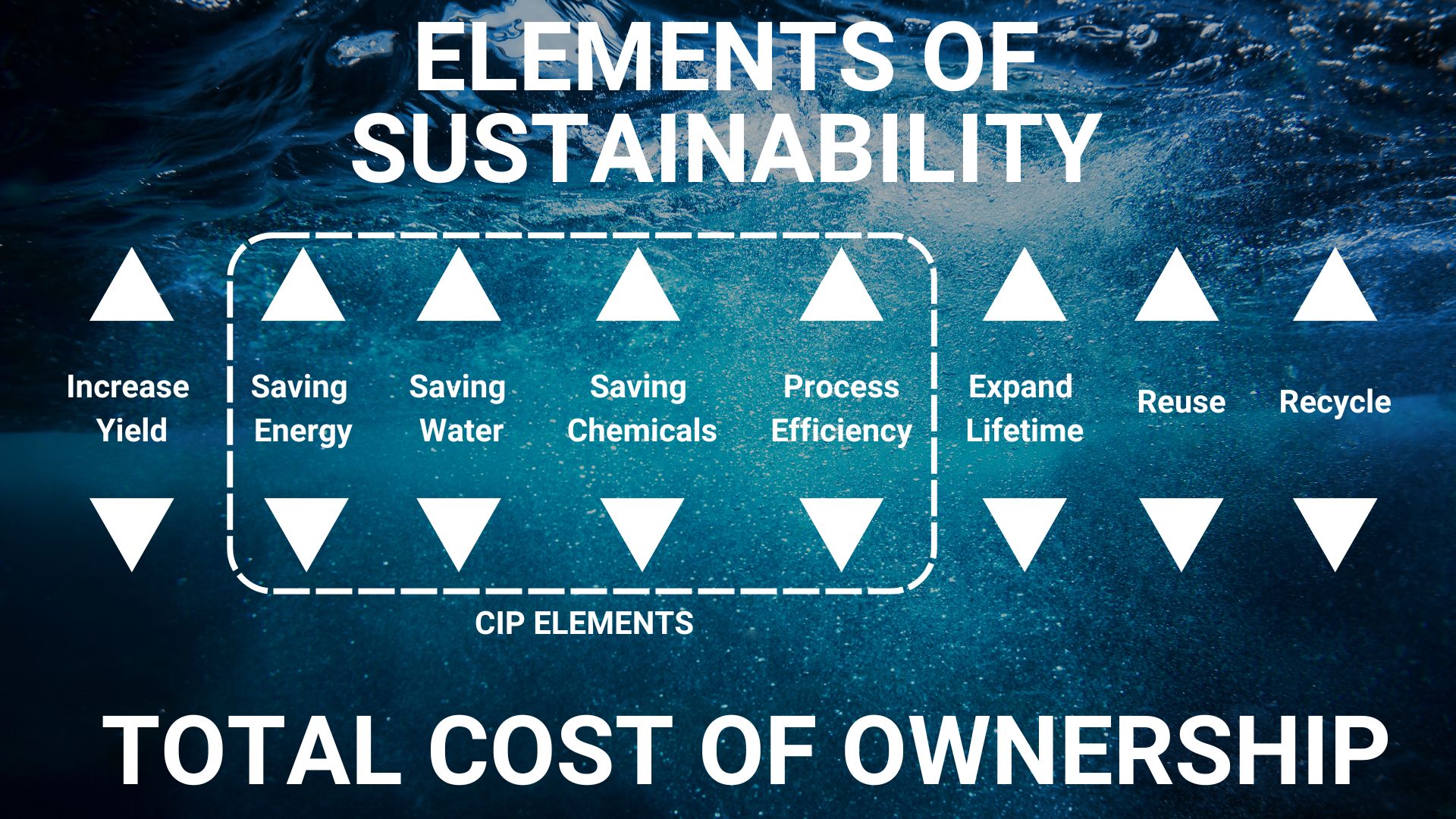
The four sustainability elements impacted by CIP:
- Saving energy
- Saving water
- Saving chemicals
- Efficiency
Analysing your CIP through modelling
In order to implement changes and improvements to your existing CIP system, you must first understand where you are at. To do this means knowing what is happening and gathering data about the existing performance of the CIP system.
Thermaflo have developed a CIP calculator model that allows the base cost to be input into the model and then based on your existing CIP process it will provide the specific costs and dollars and time relating to running the CIP.
The model factors in:
- Water used and costs
- Effluent created and disposal costs
- Water heating costs
- CIP Chemical costs
- The time of each CIP
From this, a complete picture of each circuit within your CIP is calculated, giving a basis for comparison.
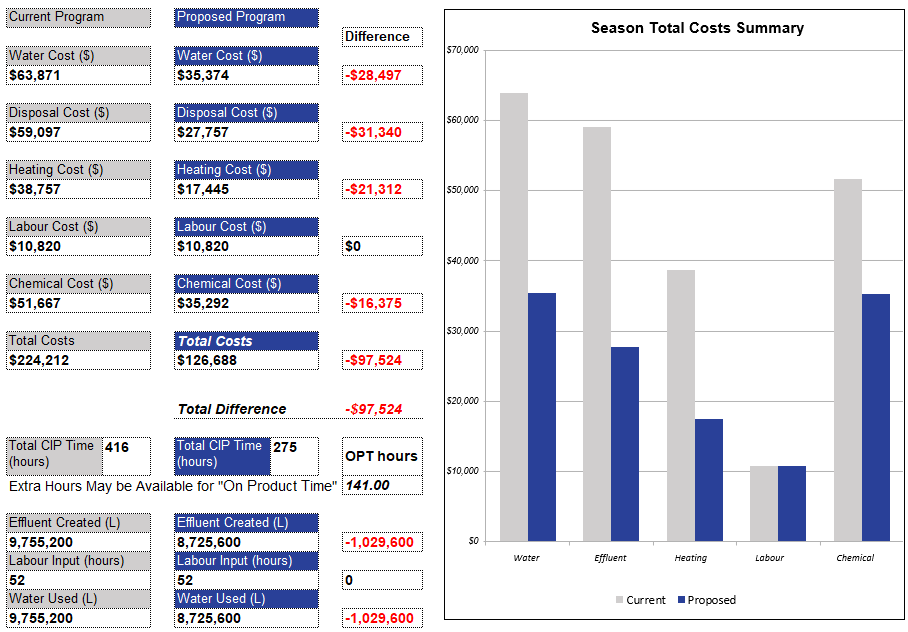
An example of the output from the Thermaflo CIP model.
In the above example, the model calculates that this CIP circuit uses too much water, energy and chemicals.
Adjusting the CIP cycle back to best practice standards will reduce the water and energy consumption, and the effluent produced.
Using the customer’s current costs, the model calculates that making these changes will save the manufacturer almost $100,000 per year.
These proposed changes also shorten the CIP time, from 416 hours per year to 275 hours. These extra 141 hours could be used for additional production time.
CIP Model Example – Dairy Manufacturer
In the example below, Thermaflo looked at the CIP system for three circuits in a dairy company.
The existing system was a single-use, and the review included the caustic and caustic-acid wash cycles.
After the model was complete, the Thermaflo process team completed a desktop study and redesigned the system as an intelligent CIP kitchen with chemical and reuse systems.
Running the redesigned system through the same model showed the following costs.
Category | Current Use | After Redesign | Potential Difference | Percentage Change |
Water Used (L) | 9,755,020 | 8,725,600 | 831,420 | -8.70% |
Water Cost ($) | $63,871 | $35,374 | $28,497 | |
Effluent Produced (L) | 9,995,152 | 5,548,400 | 831,420 | -8.70% |
Disposal Cost ($) | $59,097 | $27,757 | $31,340 | |
Total CIP time (Hours) | 416 | 275 | 141 | -33.89% |
Chemical Costs ($) | $51,667 | $35,292 | $16,375 | -31.69% |
Heating Costs | $38,757 | $17,445 | $21,312 | -54.99% |
Comparing the two sets of data shows significant savings generated by a redesign that accounts for;
- The actual plant use and capacity of the equipment,
- Modern best practice principles for CIP, and
- More efficient parts such as pumps and valves
The Thermaflo CIP model can provide objective data to demonstrate the sustainability improvement return on investment and as a mechanism for ongoing improvement.
Optimising your CIP
There are several optimizations that could be done on a plant such as this to improve the performance even further.
1. Optimization of phase separation.
It is sometimes unclear when the return solution is too contaminated to be recycled, measuring the conductivity of the returning solutions can be used to determine at what stage the solution can be recycled, what the solution needs, and when the solution needs to be disposed of.
2. Pulse rinse on tanks.
Often a constant stream of water is used in rinse steps when cleaning tanks. However, a pulse rinse can be more effective and reduce water usage.
3. Membrane filtration
These can be used to recover chemicals and water, which reduces your CIP input and disposal costs.
4. Upgrading the equipment on the CIP system
Changes to existing equipment on a CIP skid can lead to immediate savings. Significant advancements have been made over the past two years around valve efficiency. Alfa Laval has developed some very efficient technologies that offer remarkably good water and CIP fluid savings on valve washing.
5. Reviewing or adding automation to your CIP system
The key components of any CIP are:
- Time, duration of the wash
- Temperature, the temperature of the cleaning product
- Mechanical Action. CIP flowrate to ensure optimum velocity is achieved in the pipework system
- Chemistry
Having the correct automation SE / SCADA systems in place can provide the data around these parameters to give you the data you need to improve efficiencies.
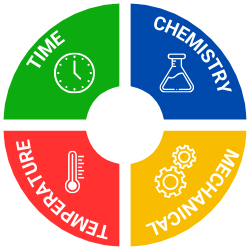
Capturing and saving the data is also helpful for CIP auditing and ensuring your plant is hygienic and cleaning effectively and allows for the system to be continually optimised.
Getting Started with CIP Optimising and Analysis
Companies investigating CIP improvements generally want to do more than simply measure and understand their environmental impact, they want to know their financial viability and return on investment on the changes being made.
The Thermaflo CIP Model allows you to understand the costs associated with your current CIP system, and you can then see the financial viability of the changes to make the system more efficient and effective.
If this has raised some questions for you, Thermaflo has considerable experience across Food & Beverage CIP systems, and can work with you to;
- Capture the data of what your CIP is doing
- Report from the CIP Model with estimated savings in terms of time, chemical, energy and water usage.
- Design a solution, and then run this through the Model to show you the ROI in dollars and sustainability.
- Evaluate it against CIP best practices and your process and sustainability goals
- Ensure you are running the best-performing CIP system for your needs
For a no-obligation chat about your CIP and potential improvements, contact us anytime.
Need A Quote Or Have Questions?
Send us an email and let us know your requirements and/or what you're wanting to achieve.
We'll take a look and come back to you ASAP.